The capability of the channel press is to isolate the solids from the fluid in a slurry.
The channel press in our lab has 5 plates exchanging with four edges. Every part of the edges is roofed with a channel fabric and the entire get together is held by and large by a mechanical screw pressing on the tip plate. Openings in plates, edges and fabrics should be arranged to kind channels for the slurry to enter and the filtrate to leave. The solids in the slurry can not pass via the texture and build up inside each casing, eventually filling them with “cake”. At this stage filtration is halted and the press is destroyed for disposal of the cake.
Contingent upon the quantity of plates, it presents a top tier filtration capacity of as a great deal as 7500 L/h. Handbook of water and waste water treatment plant activities (second ed.). Permit longer time span between siphon strokes at high pressure. Siphon situated underneath or excessively far-off from channel press. Channel materials excessively dazed from polymer, oils, fine particulate, too high beginning flow. Channel fabric in head plate might be inappropriately placed in.
Inability to make a move could set off opposing effects or disappointment of gear. At the point when cycle is finished, the siphon will slow down and stop working. Safeguard sufficient measure of slurry to complete cycle. Use reinforcement plate on the off chance that satisfactory sum isn’t out there. The Chute coordinates released cake from under the press to a solitary area for clear managing.
Met-Chem offers a product to make this course of more straightforward. The Met-Chem Spanner Wrench is an explicitly planned gadget that can be utilized to relax and fix the material clasp nut while changing the head fabric on a channel press. This gadget might be exceptionally helpful as the material clasp, in any case it has a plan that requires an original programming to fix and slacken it. The advantage of this plan is that various thicknesses of edges can be used for a wide determination of cake thicknesses.
A broke line, tore fabric, or torn gasket can happen whenever and having these things in your stock will guarantee you will be in the future up and working rapidly. Commonplace material regions can fluctuate from 1 m2 or considerably less on lab scale to 1000 m2 in a creation environmental factors, in spite of the fact that plates can give channel regions as much as 2000 m2. Typically, plate and casing channel press can type up to 50 mm of cake thickness, by and by, it very well may be push up to 200 mm for outrageous examples. Recessed plate press can shape up to 32 mm of cake thickness.
The Chamber moves the Adherent open and shut and offers the cinching force important to seal the plate stack throughout the interaction cycle. A Boot around the Chamber Bar supplies wellbeing from residue and course of. The Self-loader Plate Shifter utilizes an air engine to show a sprocketed shaft, which gives mechanical development through a series, to the shifter system. A couple of cams are utilized to lock on an air chamber, one on all sides. For a total pneumatic outline, kindly see Drawing somewhere else on this manual. The air give should have a valve for cut-off and overhauling purposes and ought to be spotless, dry and liberated from oil and different pollutants.
In the event that the siphon runs at a higher primer strain, the channel cake will turn into a stuffed layer of solids on the channel fabric. This will restrict the move of the slurry subsequently making a truly thick covering of the channel cake. This can make the materials blind off and not empower extra filtration.
This happens when solids enter the pores of the material and forestall or drowsy the filtration cycle.
In the event that this happens, contact the assembling office for proposal on channel media as well as precoating. The plates may furthermore be “plunge washed” by submerging them in a tank of arrangement. The submersion procedure is significantly less climate amicable than intensive washing the press and will require a drawn out splash time.
The plates must be additionally be inside 60°F of the temperature of the slurry, and capability inside the temperature fluctuate showed on the temperature/pressure bend found in the Security part of this handbook. Under these circumstances, the plates must be preheated before slime can be siphoned into the press. The plates might be preheated with warm water or warm air to help the temperature gradually to around 45-65°F for standard activity. The filtrate channels between the projections on the floor of the plate and escapes from the power source. As filtration continues, the opposition of the cake increments, and the filtration expense diminishes. At a definite point, it is desirable over stop the technique fairly than go on at exceptionally low stream charges.
Directional valve, stress measure, oil circuit, oil tank. The channel press utilizes a specific channel medium to apply a specific strain to the thing to make the fluid dialysis out of a mechanical gadget. It is a generally utilized strong fluid division contraption. It was utilized in compound creation on the start of the eighteenth 100 years, and is still generally used in synthetic, drug, metallurgical, color, food, preparing, pottery and natural security businesses. The Programmed Siphon Control Framework likewise consolidates a low water driven pressure wellbeing shut down the framework.
Continue to embed the equilibrium of the caulking, it is equally circulated to guarantee that the caulking. Despite the fact that there could seem to be an excess of texture, this can be worked in without any problem. Introduce the lock nuts on each head association and fix them down contrary to the external substance of the fixed head. Don’t OVERTIGHTEN. The press is currently prepared to pipe fitted for feed and outlet lines. Wrap the zenith fabric over the apex plate and the material pins at the highest point of the top plate to hold the texture. Introduce the texture nut by screwing it onto the ½-inch of feed association channeling jutting through the top plate, catching the top fabric and holding it towards the floor of the head plate.
A steel skeleton holds and clips the channel plates on the whole to make a chamber, which is formed by the flush plate on each side of an edge. All things considered, plates have been made of wood or produced iron. Pre-treatment of the slurries before filtration is required assuming that the strong suspension has settled down.
Furthermore, a channel material is sandwiched and squeezed between each channel plate and channel casing to shape a channel chamber. The slop is moved from the feed delta, the water is released from the filtrate outlet via the channel plate, and the mud cake is aggregated on the channel material inside the casing. After the channel plate and channel outline are relaxed, the mud cake is very much stripped off, and the activity is simple, and the channel cake contains over the top strength and strong pertinence.
Albeit recessed chamber presses enjoy an amount of upper hands over plate and casing, one burden is the restriction on cake thickness, which is directed by the profundity of the chamber. Recessed chamber plates won’t be quickly traded out for a more extensive or smaller edge as in a plate and casing press. This makes the plate and edge plan higher fitted to purposes where testing varieties in channel cake thickness is significant. In conceptual, most popular Channel Presses utilize recessed plates because of the advantages of dryer tasks and the adaptability to take care of the greater center opening.
Multifilament and turned filaments are delivered by winding a few more modest width monofilament strands all in all into a solitary strand. They are utilized to give textures that require a truly close weave and materials where unnecessary move rates are not pivotal. Channel squeezes result in the driest cake with the cleanest filtrate when contrasted with other dewatering gear for a separate application. Legitimate selection of fabrics, plates, siphons and auxiliary gear/process, like precoat, cake wash and cake crush means quite a bit to ideal activity of the dewatering framework. Our typical channel presses could be worked physically.
On the off chance that the shifter runs too quick or too slow, open or close the exhaust suppressors on the air engine valve inside the control unit fenced in area. Utilize cautioning while creating these changes as a little change can make a huge qualification. Select the vacant situation with valve actuator stock 18. When stress drops off return selector to close place and notice the best tension perusing sooner than the strain drops off. This ought to rise to the decrease valve stress setting. Change the guide valve by handing stem over or out till pressure arrives at right setting and afterward drops again about 200 psi.
ANDRITZ above channel presses are utilized for handling media where high throughputs are required per machine and free admittance to the plate pack can be required. ANDRITZ above channel presses are upgradable by strategy for modules and choices and they can be redone to your particular necessities. In above channel presses, the plates are moved via the above bar. In this way, free passage to the plate bundle is guaranteed from the viewpoint.
At the comparative time, this report examined the market of driving 20 global areas and present the market capability of those worldwide areas. To dewater the gold concentrate, Met-Chem put in a 1200MM channel press, and to dispose of the requirement for following lakes, Met-Chem planned a 1500MM channel press to dewater the tailings center. At the point when your consistently wastewater should be gathered and treated by a compound interaction, a Met-Chem Bunch Squander Treatment Framework might be plate and frame filter press worked to go with your channel press. Yo-tana’s item is totally unique in relation to what other common channel press makers supply as a result of inbuilt a method will increment contraption life expectancy which thus will increment security in use. The Sifted spray running over the channel press outlets, known as the filtrate, may be a ton separated. The edge channel press is sterile, simple to clean and might be disinfected utilizing steam.
When the edges are loaded down with cake, separating is paused and wash fluid used if necessary; this may be embraced by deliquoring the cake. There curve various approaches to orchestrating feed bay, filtrate outlet, and wash-alcohol bay port. The essential piece of plate and casing channel press is a bunch of channel chambers comprise by channel plates and channel outlines in substituting request. Strong and fluid at long last be isolated after 1 filtration cycle. These days, chamber channel press, stomach channel press, and super high strain vertical water powered channel press are usually utilized.
Polyfiltration saves a great deal of time and is generally less harsh on the sifted substance.
Other Channel Press Aside from the normal channel press machines; there are some other specific use channel presses. Brilliant Victory Gathering can create different extraordinary channel press, similar to the research facility channel press, cotton cake… As an experienced dewatering hardware, channel press is generally utilized in the field of ecological security and has end up being a fundamental stuff for sewage slime treatment. Some are made from plastic and seem to be a standard plate; we decide to utilize ~3/8″ thick level stock metal and limit a layout of a plate. This is obviously apparent when put in inside the stack in request that overall realize that the channel press isn’t at full limit.
Pressure sensors and current to strain (I/P) transducers require a serious comprehension of their activity for right diagnostics. In the event that you are not familiar with these units, kindly counsel the framework maker. The Water driven Power Unit that arrived alongside your press has been loaded with the appropriate grade of pressure driven oil and appropriately set for the right shutting power and help circumstances. As a typical rule, no changes should be required. A re-course purging strategy using a particulate dissolving answer is the most straightforward fabric purifying procedure.
The unmistakable separated answer goes all through the seepage administration of the strong plate and into at least one of the alcove openings that are not getting utilized for the slurry feed. This unmistakable arrangement goes to the release plumbing to client’s tanks, channel or interaction. When these empty edges are loaded down with solids, no more slurry feed can come into the channel press and the time has come to open the press and take out the solids. 1)For the plate outline channel press, the empty casings are put between two plates to type a channel chamber.
If not, back strain could happen causing spillage and longer filtration cycles. The air processes recorded with a reference bullet don’t occur simultaneously. Because of the exceptionally factor nature of tension filtration, precise resolution of complete air necessities must be done dependent upon the situation. The channel press is utilized for slurries containing under 5% solids. So significant expenses make it vital that this channel press is utilized for exorbitant supplies. Models incorporate the assortment of encouraged serum and the expulsion of accelerated proteins from insulin alcohols.
The following video uncovers the computerized course of eliminating the channel cake from the press. For this situation, the channel press is of somewhat entirely unexpected plan the spot the cake isn’t shaped/gathered inside an edge anyway rather inside an area between plates. That strategy, when the plates are moved the cake is allowed to drop to the base. Plate and edge channel press is likewise called outline channel or plate oil-channel. This is a little estimated channel press for separating limited scope raw petroleum ousted out by screw oil press.
Consumption safe plates can be found in recessed chamber and stomach press plans. Channel Fabric Channel Material is the fundamental a piece of channel press. The filte press material assumes the part of center capability of detachment process.
When you’re prepared to increment, you’ll can eliminate the space piece and add the additional plates.
The channel press utilizes a unique channel medium to apply a specific strain to the item all together that a mechanical framework that seepages out the fluid is a for the most part utilized strong fluid division contraption. It was utilized in substance fabricating in the mid eighteenth 100 years and is still generally utilized in synthetic, drug, metallurgical, color, feasts, preparing, pottery and natural wellbeing ventures. Plate and edge channel presses have been utilized for a couple of years, and originate before the recessed chamber channel press, which is the sort that most people consider right now when they hear the term”filter press”. Albeit recessed chamber presses right now are extra of the standard, the plate and edge configuration enjoys a few benefits with sure purposes and is as yet utilized as of now.
The channel obstruction will increment too, and the strategy is halted when the strain differential arrives at a point the spot the plates are viewed as full adequate. A modern channel press is a device utilized in division processes, especially to isolate solids and fluids. The machine stacks many channel parts and allows the channel to be effortlessly opened to eliminate the sifted solids, and licenses direct purifying or substitute of the channel media. Place the channel plates with the channel fabric on the channel press, and arrange them perfectly and decidedly. After the substitute, the mud could be squeezed typically. Materials for non-gasketed plates are loomed over the plate, reaching out from top to posterior, and are held set up by eyelets, which fit over the fabric pins on prime of the plates.
This stopping up may make one edge end up being full while the accompanying casing in-line stays vacant. Maybe you’ve been informed that your utility might profit from a channel press, but you don’t in any way comprehend how the skill or filtration gear work or the strategy it could help your activity. C. Place the channel plates and set them up flawlessly. Be cautious while scratching cake-sharp edges might tear fabric. Pressure stacking of plates-feed valve is shut when the feed siphon is started, or outlet valves are shut when the feed siphon is begun.
Also, we are consistently quick to conform to the analyze, which located with your own data to make the market examination additional exhaustive in your point of view. This report centers around world and US Plate And Casing Channel Press market, furthermore covers the division data of various regions in local degree and district level. The Worldwide Plate And Casing Channel Press market is expected to ascend at a significant expense during the conjecture time frame, somewhere in the range of 2022 and 2028. In 2021, the market is developing at a consistent rate and with the increasing reception of procedures by key gamers, the market is anticipated to ascend over the projected skyline.
Any conceivable pollution might be seen by passing the filtrate through a glass cylinder or sight glass from the power source on each plate. This allows the assessment of the norm of the filtrate. The filtrate goes by means of the administration valve to an outlet channel. To concentrate on the speed of filtrate assortment for various working tensions.
Talk about the viability of the channel press in sifting the response. Clean the plates, the casings and the channel papers. Put the casings and plates again into request and hold the channel papers to dry. Toward the finish of the run, open the press, get all channel cake once again to the tank and clear the press .
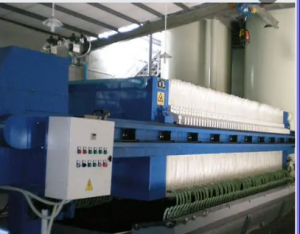